歴史にみる模型飛行機の顔さまざま
(11) 新素材(1960~)
歴史
図1 現代の新素材を使った国際級ゴム動力機(説明は機種より機尾へ)
①機首開口部:軽金属機械加工のノーズブロック取り付け材
②前部胴体(動力ゴムが入る部分):カーボン・パイプ
③主翼取り付け台(パイロン)には多機能タイマーがつく
④主翼:骨組みは新素材とバルサの混用、フィルム張り
⑤胴体継ぎ手:軽金属機械加工、前部胴体に細い後部胴体パイプをつなぐ
⑥尾翼構造は主翼に準じる。垂直尾翼は透明フィルム
⑦水平尾翼取り付け具も精密軽金属加工機
1. はじめに
プラスティックスや複合素材などの、いわゆる新素材は、年を追って性能は向上します。バルサやヒノキのような天然材は、何万年前から材質・特性は変わりません。昔は天然材しかありませんから、その中で性能のよいものや相性の良いものが選ばれて、当該生産物の材料になります。そういう事情で飛行機や模型飛行機が、取りあえずスプルースやヒノキで作られたわけです。
模型飛行機に付いては、発達の途中の1930年頃に極めて相性が良いバルサ材が発見されたので、それが急速に普及して独占的な主用材になりました。模型飛行機の構造との相性が抜群であったため、急激に材料の転換が生じたので、「バルサ革命」と言われることもありました。
本稿の第5回「バルサ革命」はその状況であり、第6回「室内機」と,第7回「模型空気力学」はその余波として生じた模型航空界の新しい展開です。
バルサ材の有利さが隔絶していたので、しばらくはその独占状態が続きました。少なくともバルサ材が豊富に手に入った米・英などではそうでした。
しかしながら、「器用貧乏」と言う言葉があるように、万能材よりも「適材適所」のほうが結果は良いようです。日本では、「オール・バルサ」よりも適所にヒノキ材や竹ひごなど国産の優秀材を組み込んだ混合構造が主流でした。
このような環境に、日進月歩の新素材が参入します。自然の流れとしてバルサ材の用途が蚕食されていきました。但し、「プラスティックス」と複数形で書かれる様にプラスティックには多くの種類があります。その複合材は2乗倍くらいの種類になりますから、最適な用途も限定的であり、バルサ材のように在来の全ての材料に代わり独占するわけではなく、新製品が開発されるたびに、種類ごと、最適専門分野ごとに、徐々に代替されたわけです。だから、「バルサ革命」に対する総入れ替えの反革命ではなく、部分的な修正です。
「新素材」の「適材適所」への進出として、以下のように大別します。
(1) プロペラ
(2) その他の射出成型部品
(3) フィルム
(4) FRP(ファイバー・レインフォースド・プラスティックス/グラスファイ
バーやカーボンファイバーで補強し、プラスティックで固めた構造体)
(5) フォーム・プラスティック、スチレンペーパーなどの軽量材
(6) カーボンシートなどの補強材
(7) カーボンパイプなどの部品
(8) その他
(9) 以上のプラスティック系のほかに、精密加工された金属の部品が模型
飛行機に使われるようになりました。「新素材」ではありませんが、
便宜上ここで取り上げます。
上記の項目は、モデラーが当該新素材にどこの工程から関わるかで大別されます。つまり完成部品か、材料(糸・シート・板・ブロックなど)か、材料を作る素材(モノマーなど)か、と言うことで、後ろに行くほど高度な関わり方になります。だから、モデラーが模型飛行機に新素材を取り入れた順番としては、前からだったと思います。
2.プラスティックのプロペラ
1950年代のエンジン機のプロペラは、サクラ、ホウなどを機械で削り出し、直径・ピッチ別に市販されていました。プロペラはエンジンの圧縮行程に合わせて、水平位置で停止するように取り付けてはいましたが、それでも垂直位置で停止して、着陸のときに折ることが度々ありました。当時のプロペラは消耗品だったのです。
図2 エンジン機のプロペラ
フリーフライト種目も同じような環境でした。高度成長前で、まだ貧乏であった日本のモデラーは、性能もよくなるので、自分でホウ材からプロペラを削り出していました。浜松で日本選手権大会が開催されたとき、東京発の鈍行列車のなかでプロペラを削っていたと言う逸話が残っています。
そういう環境に「折れないナイロン製のプロペラ」の登場は、衝撃的でした。木製プロペラの数倍の価格で、直径・ピッチなどの仕様も限定されていましたが、競技の全ラウンドを飛ばし抜ける保証は大きなメリットでした。
図3 エンジン機のプロペラ(その2)
少し遅れて、プラスティックの射出成型のゴム動力ライトプレーン用プロペラが登場します。在来品はホウ材を機械で削った物で、おおむね直径10~30㎝の範囲を3㎝おき位の品揃えで売られていました。ピッチは明示されていませんが、おおむねピッチ比1前後でした。複数のメーカーがあり、ブレード幅・平面形・ピッチが微妙に違い、差別化がありました。
ライトプレーンの重さと速度では着陸時にプロペラを折損することは無かったので、メリットは売り手側のコストや生産性にあったようです。ユーザー側のメリットとしては、そのままでそこそこの性能を発揮できる点が挙げられます。木製プロペラの中には、仕上げや修正を必要とするものが有ったからです。
なお、キットに入っているプラスティック・プロペラには、次項「その他の射出成型部品」に含まれるプラスティック製「コメタル」が付属していました。「コメタル」は和製英語で、プロペラを一本胴に取り付ける軸受け部品のことです。幅4~6㎜、厚さ1㎜位のアルミ板を「コ」の字型にまげて、端にプロペラ・シャフトの穴を開けた「メタル」(金属軸受け)が語源と言う説と、郵便切手大で厚さが4~6㎜の板の一辺にシャフトの通る穴をあけた代替品を「木メタル」と呼んだものが訛ったという説があります。
この時代は、コメタルを胴体前端に接着し、糸を巻いて補強しましたが、プラスティック製のコメタルは胴体に断面形の穴が開いていて、そこへ前端を差し込むだけで済みますから、取り付け作業は簡単です。
エンジンは年を追って高性能になり、回転数は2~3倍、出力は1桁以上向上しています。プロペラには物凄い遠心力が加わりますから、在来の木や単体プラスティックでは耐えられず、回転中に破断して飛散する危険が生じます。このような高速回転をする高性能エンジンに付けられたプロペラの先端速度は音速(330m/秒くらい)に近いので、ちぎれた破片はピストルの弾丸に近い初速で飛び散ります。
この危険性に対処するために、ガラスやカーボンの繊維で補強したプラスティック・プロペラが開発されました。簡単に言えば、プロペラの形をした雌型に繊維を入れて、隙間にプラスティック液を流し込んで固め、成型したものです。遠心力方向に丈夫な繊維が通っていますから、高出力・高回転に耐えられます。
3. その他の射出成型部品
鋳物や射出成型品は、一工程で複雑な形の部品を作れます。たとえば、複数の部品を張り合わせて作る部分を、一挙に形に出来ます。その代わり、型やジグを必要として、これらを製作する費用や手間は非常にかかり、それを回収するためには同じものを沢山つくる必要があります。だから、個々のモデラーには手に負えず、メーカーの領分になります。
メーカーにしても、生産量を上げるためには汎用性のあるものが優先されるでしょう。前項のプロペラも本項の同類ですが、寸法が規格化されていて、さまざまな設計の機体に共通に使えるから採算にあうわけです。
他方、モデラーが自作に多用するバルサ材はきわめて軽い代わりに軟らかく、集中荷重を受けることが不得手です。たとえば、ピアノ線の脚を取り付ける場合、着陸するときの衝撃を受けるには広い範囲に荷重を分散しなければ、接合面が破断します。
このような場合、プラスティック部品を間に挟むと、荷重の分散が容易です。つまり、広い接着面と、ハリガネを固定する穴のある「脚の取り付け部品」ならば、硬いプラスティック材でハリガネの集中荷重を受け止め、それを広い接着面に分散してバルサ構造に伝えることが出来ます。
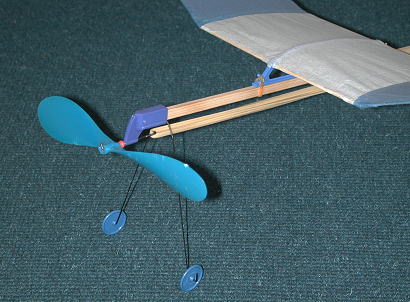
図4 普通の市販キットのライトプレーンのプラスティック部品
プロペラ、コメタル(プロペラの軸受け)、車輪、主翼取り付け台
前節で触れたライトプレーンのコメタルも、動力ゴムの張力や、着陸や衝突のときの衝撃を、破損を起こさずにしっかりと胴体に伝える部品です。エンジン、脚、操縦システム(舵を動かすロッドなど)集中荷重のかかる部分、言い換えれば金属など強度が格段と大きいものの取り付け部で、荷重を上手にバルサ構造に伝える部品には、プラスティックの完成部品が約に立つわけです。
4. 被覆用フィルム
翼面などを被覆するプラスティック・フィルムも盛んに使われています。模型飛行機用に開発された専用フィルムが、模型店などで市販されていますが、包装用、ラップ用などの汎用フィルム、コンビニの袋、雨天のときの新聞配達に使われている包装フィルムなど、一般品の利用も行なわれています。室内機用に極薄のもの(汎用品?)も、使われています。
プラスティック・フィルムはそれ自体が防水性・耐燃料油性を持っていますから、紙や絹など在来の被覆材のように塗装する必要がありません。従って、プラスティック・フィルムを使用すると塗装工程を省略できて、機体の製作の能率が向上します。
在来品の紙(和紙)には収縮性があり、塗料との組み合わせによって適度に緊張させ、翼の捩れ剛性を得ると言う効果があります。汎用フィルムの転用の場合はその効果が期待できないので、骨組みを捩れ難い特殊構造(斜めリブなど)にする必要がありました。
模型飛行機用の専用フィルムは、熱収縮を利用して緊張を加え、普通構造でも捩れ剛性が得られます。但し、小さなアイロンなどの加熱道具を使って被覆作業を行なう必要があります。
同フィルムは、厚手(大型機用)が先行し、薄手(小型機用)に展開しました。透明・不透明、色なども、選択できる幅を広げています。しかしながら、塗料を混ぜて作る中間色はありませんから、色彩デザインは制約されます。そのあたりに「紙派」との棲み分けがあります。
図5ハイテク・ライトプレーン(自作機)の新素材とその細部
胴体はカーボン・パイプ(釣竿?)プロペラハブは可変ピッチ式、翼はフィルム張り図5-2拡大した可変ピッチ式プロペラハブ
5. FRP(ファイバー・レインフォースド・プラスティックス)
プラスティックを、グラスファイバーやカーボンファイバーで補強して固めた構造を、FRP(ファイバー・レインフォースド・プラスティックス)と言います。型にファイバー(繊維)を巻きつけ、それにプラスティック溶液を塗りつけ、あるいは流し込み、乾燥・硬化後の型から外せば、薄肉で複雑な形の三次元の部品が作れます。
実物の小型舟艇(ボート、ヨット)や模型船舶などの船体は、この方法で作られているものが沢山あります。前述した高出力エンジン用のプロペラも、FRPです。RC機の胴体などには、相性のある工法といえます。
型は、木や石膏などモデラー個人の手に負えるものですから、自分の設計に基づく個人の一品生産も可能です。市販完成品の胴体や船体をそのまま型にして、一回り大きなコピーを作るウラワザもあるようです。
6. フォーム・プラスティック、スチレンペーパーなどの軽量材
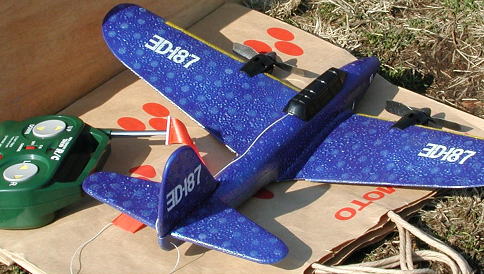
図6 発泡スチロール製トイRC機
プラスティックを固めるときに発泡剤を混ぜておけば、スポンジ状に固まり、嵩比重が極めて小さいブロックになります。比重は発泡の程度によってコントロールできますから、軽いものはバルサ材よりもさらに軽い比重が0.1以下のものも作れます。
空気は優秀な断熱材ですから、スポンジ状のプラスティック板は一般的には建物の断熱材として販売されています。また、パソコンや家電品などの箱詰めの充填材や、鮮魚などの冷蔵輸送箱にも利用されています。
このスポンジ状プラスティックは低温で溶けますから、ニクロム線に低電圧をかけた道具で容易に切断できます。刃渡り15cmくらいの普通の糸鋸の弓枠にニクロム線を張り、電池数本の電圧をかけた切断具が市販されています。
カッターやノコギリでも切断できますが、仕上がりは上記の熔断法が綺麗です。
1000×300×60㎜位の大きなフォーム・プラスティック材から、RCやUコンの大型機の片翼を丸ごと熔断法で切り出し、中央を繋いで組み立てる工法があります。多くは切り出し済みの市販品ですが、特殊寸法に自作する人も居ます。そのときは、弦の長さが1mくらいの大きな弓を作り、翼の付け根と翼端に翼断面の型板を当て、サンドイッチ法(第5回「バルサ革命」参照)の要領で一気に熔断します。このような大きな部品も作れますが、専用の接着剤で容易に接合できますから、胴体を左右半分ずつ作り、中をくりぬいて中央で接合し、中空胴にすることも簡単です。
フォーム・プラスティック、スチレンペーパーなどの軽量材は、小さなトイRCから、室内スタント機(F3Q級)、さらには上記のような大型機まで、広い応用範囲があります。同じ材質を、厚さ1㎜位に加工したスチレンペーパーも、小型のライトプレーン式入門機や、上記のトイRC機の翼として沢山使われています。
適当な平面形に切り抜いて、上に折って上反角を付けた平板断面翼型でも十分に飛びます。少し手間をかけて、コード中央付近で「へ」の字型に曲げた翼型だと、強度・性能とも向上します。トイRC機は厚みのあるフォーム・プラスティックの胴体と、ライトプレーンはバルサなどの棒材の胴体と組み合わせます。このほかに、同じスチレンペーパーで立体折り紙式に中空の胴体を作って、動力ゴムを中に取り付けたものもあり、この形式だと1種類のスチレンペーパーだけで機体全体が作れます。
図7 1mm厚スチレンペーパー製小型ゴム動力機の機首
本体のほか、プロペラ、機首ブロック(発泡プラスティック材)も新素材
7. カーボンシートなどの補強材とカーボンパイプ
カーボン繊維を織った、厚さが0.5㎜位のシートが市販されています。このシートは単体でも丈夫ですが、細いバルサ材などに接着して複合材にすると、相乗的に強度と剛性が大幅に向上します。
ゴム動力の中型機以上の後縁材は、昔は3×10~15㎜のバルサ材を楔(くさび)型に削ったものが定番でしたが、現在では2㎜角のバルサ材にカーボンシートを貼り付けたもので済んでいます。ライトプレーンの一本胴でも、バルサ材にカーボンシートを張ると、同寸のヒノキ棒に匹敵する強度が得られるようです。ヒノキ材の比重はバルサの3倍くらいありますから、重量も軽減されるはずです。
最近のフリーフライト滞空機は、昔に比べて格段と主翼スパンが長くなり、縦横比が大きくなりました。特にFAIの3種目(F1A、F1B、F1C)では目立ちます。縦横比が大きくなれば抗力が減り、滞空時間が増えることは昔からわかっていたのですが、そうすると主翼の強度がもたなかった事情がありました。最近になってできるようになったのは、カーボンシートの補強が効いたためだと思います。つまり、カーボンシートをうまく使い、バルサ材と複合材にすると、飛行性能がかなり向上するのです。
図8 胴体にカーボンシートを貼り付けて補強した手投げグライダー(下側から見る)
同じカーボン材で小径のパイプ材も利用されています。釣竿やゴルフクラブに使われているものと同類ですが、より薄肉で軽量なものが選好されているようです。そのまま胴体に、あるいは極小径のものが主桁や前縁材に使われていますが、強度的には過剰で、通常の使い方で壊れることはなさそうです。
昔の胴体は、尾翼の直前でも20~30mmの太さでした。だから、尾翼が胴体に重なる部分や、周りの気流の乱れのために、尾翼の効かない部分が公称面積の10%以上生じるといわれていました。カーボンパイプを胴体に使うと、太さ5㎜位で強度的には十分ですから、尾翼の乱れや陰はほとんどなくなり、モロに効くことになります。従って、一回り小さな尾翼にして、浮いた面積を性能向上のために使うことが出来ます。
8. 金属の精密加工品
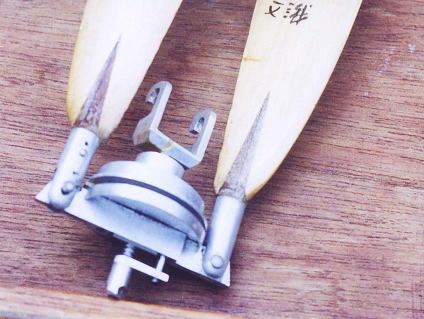
図9 金属加工部品:プロペラハブ
金属は昔から存在し、模型飛行機の部品にも使われてきました。いまさら「新素材」の仲間に入れることも無いのですが、使われる形に大きな差が生じたので便宜的に本項の顔に含めます。
昔のゴム動力模型飛行機の金属部分としては、プロペラのシャフトのピアノ線と、その軸受け部分くらいでした。少し時代が下ると折りたたみプロペラが登場して、その折たたみヒンジ(蝶番)部分に金属が使われます。金属加工用具としては、針金切りついたペンチが大・小あれば用が足りました。
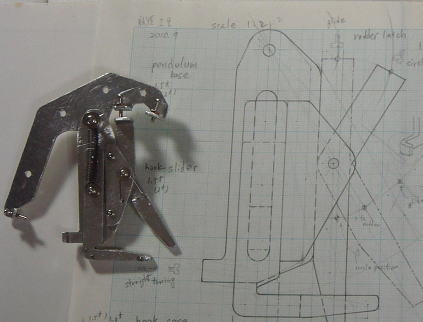
図9-2 金属加工部品:特殊曳航フック
今でも大半はそれで済みますが、人によって格差がついてきました。卓上の旋盤・ミーリング機などの小型工作機械が手ごろな金額で手に入るようになり、やる気のあるモデラーはこれらを使って性能向上を図ろうという流れが生じました。
フリーフライト種目は、文字通り「何もしないで自由に飛行させる」ものですが、タイマーなどを使ってきめ細かく管理する傾向が主流となりました。RCやUコンは、フリーフライト以上にメカニズム化指向が強い種目ですから、当然同様の傾向を示します。
結果として、今まで簡単な工具を使ってシロウトが作っていた回転部分は、精密なベアリングがそれなりの精度で取り付けられ、運動部分もがたがたの穴からきっちりした結合に変わりました。
これらの多くは、購入部品ですから、手作りであった機体に高性能な新素材が組み込まれたのと同じような影響を与えたのです。
9. 新素材の評価
バルサ革命の結果、模型飛行機がバルサ材と、カミソリの刃と、1種類の接着剤だけで作れるようになった・・・・と言うのが、抽象化された筋書きです。現実はいくつかの但し書きを加えなければなりませんが、新素材を導入する前の初期状態のモデルとしては十分です。
そこへ、いわゆる「新素材」が入ってきました。その性能・特性は、全ての点でバルサ材を上回っているのではなく、部分的な利点と、抱き合わせになった欠点を持っています。だから、利点を生かすような部分的な使い方になります。
従って、工具・工法・接着剤などが複数種類・複数系統だけ必要になります。モデラーは、これらを新たに調達し(模型店以外の商品もあります)、作り方などを勉強しなければなりません。新素材の利用には、それなりの犠牲や費用を伴うのです。
国際級競技のような高水準の場では、オール・バルサのような汎用材だけで作った機体では、勝負にならなくなってきました。従って、否応無しに新素材を導入しなければならないのですが、一般のモデラーが簡単に出来ない技術や設備を必要とするものも有ります。
並行する流れに、BOM制(自作機規定:第8回「模型飛行機はホビーとスポーツの複合活動」参照)の廃止と市販完成機の競技参加の許可と言うことがあります。つまり、工場などで専門職人が、多くの新素材を専門設備・専門技能を使って市販完成機に利用し、一般のモデラーでは容易に作れない高性能機を作ってしまったため、汎用材による自作機が競争力を失ってしまったのです。
模型飛行機の楽しみ方が、設計・製作・飛行という連続技であるため、設計・製作を自分で行なうことを楽しむ一派にとっては、上記のように新素材は「痛し痒し」の両刃の刃です。オール・バルサ時代は、手元の材料で手早くさまざまな設計を試み、その差異を見つけて楽しむことが出来ました。現在、それを楽しめるのは国際級のように絶対性能を追いかける種目ではなく、国内級や公園で楽しむ草の根種目になってきています。新素材の評価・利用は、模型飛行機の楽しみ方の選択とも関わって居るのです。
編集人より
大村和敏氏は元模型航空競技・ウェークフィールド級日本選手権者であり、模型航空専門誌にも寄稿されています。